The Rise of Custom Flange Solutions in Specialized Industries
- huasenmetalcast
- Apr 29
- 11 min read
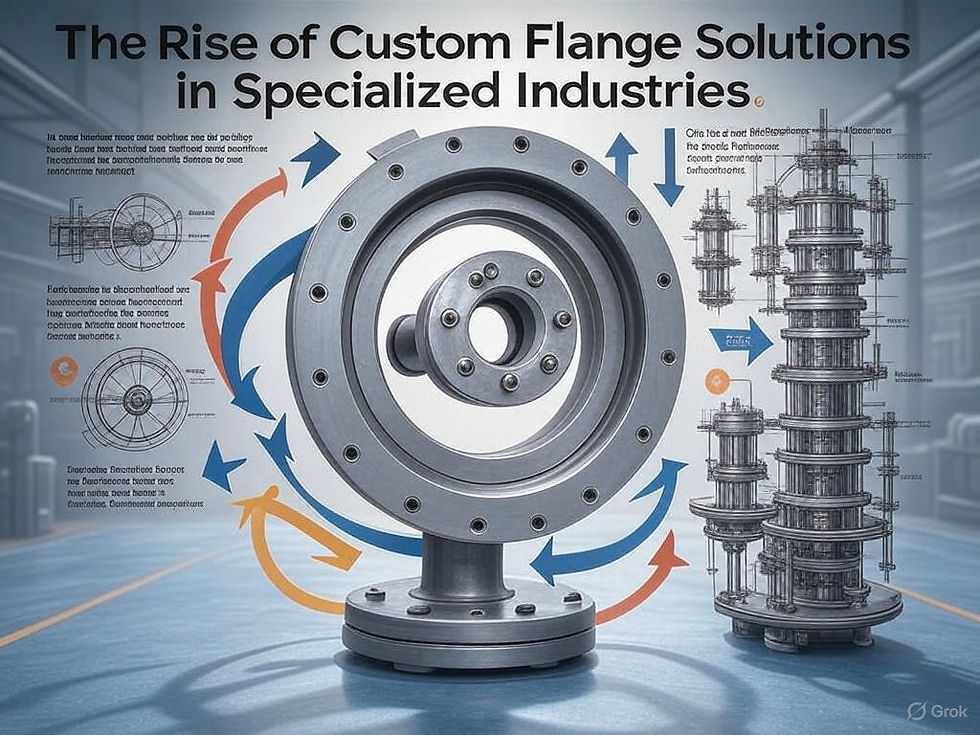
Introduction to Custom Flange Solutions
What Are Custom Flanges?
Custom flanges are specialized connection components designed specifically to meet the unique requirements of particular engineering systems. Unlike standard flanges, which come in predefined dimensions and specifications, custom flanges are tailored to match specific operational conditions, design constraints, and industry standards.
In essence, a custom flange is crafted when a project’s demands cannot be fulfilled using a regular, off-the-shelf product. These flanges may vary in size, thickness, material composition, pressure ratings, and connection types. Whether it's a non-standard diameter, an unusual face type like a special groove pattern, or a material designed to withstand extreme environments, custom flanges offer engineers and designers the flexibility they need to build more efficient, reliable systems.
Custom flanges are not a luxury in today’s engineering landscape—they're a necessity. As industries become more specialized and systems become more sophisticated, the one-size-fits-all approach falls short. Customization ensures optimal performance, extends service life, reduces maintenance, and often enhances safety across various applications.
The Evolution of Standard to Custom Solutions
Historically, the flange industry operated on the principle that standardization was the most effective way to ensure compatibility and efficiency. Standards like ANSI, ASME, DIN, and JIS defined dimensions, pressure classes, and material requirements for flanges used globally. These standards served industries well during periods when technology was relatively stable, and project requirements were less complex.
However, as industries such as aerospace, chemical processing, renewable energy, and subsea exploration evolved, so did their needs. Off-the-shelf solutions could no longer address the nuanced challenges presented by these rapidly advancing fields. Factors such as extreme pressure, corrosive environments, high vibration, thermal cycling, and unique spatial constraints highlighted the need for more specialized connection solutions.
Manufacturers responded by developing the capability to design and produce custom flanges. Advances in computer-aided design (CAD), simulation technologies, and precision manufacturing techniques have made it easier and more cost-effective to produce custom components tailored to each project's specific needs.
Today, the transition from standard to custom solutions represents not just a trend but a paradigm shift in engineering. Companies no longer settle for "good enough" when a perfect-fit solution can significantly improve system performance, reliability, and cost-efficiency.
Why Specialized Industries Demand Customization
Specialized industries operate under stringent performance, safety, and regulatory standards. In these fields, the stakes are incredibly high: a single failure could mean environmental disaster, loss of life, or catastrophic financial losses. Standard flanges, while robust, often cannot meet the extreme and specific conditions present in these industries.
For instance, aerospace applications may require ultra-lightweight yet high-strength flanges made from exotic alloys. Offshore oil drilling operations need corrosion-resistant flanges capable of withstanding both high pressures and the corrosive effects of saltwater. Pharmaceutical production environments demand flanges manufactured to sanitary standards that ensure no contamination.
Customization allows these industries to address:
Extreme Environmental Conditions: High pressure, high temperature, or highly corrosive atmospheres.
Unique Design Constraints: Space limitations, weight restrictions, or specific flow requirements.
Stringent Compliance Needs: Meeting industry-specific standards like API, ISO, or FDA regulations.
System Integration: Seamless compatibility with non-standard equipment or proprietary designs.
Ultimately, custom flange solutions empower specialized industries to push boundaries, innovate safely, and maintain the highest levels of operational excellence.
The Growing Need for Tailored Flange Solutions
Complex Engineering Requirements
Modern engineering projects are far more complex than those of previous generations. As industries push deeper into hostile environments—whether it’s exploring the ocean floor, expanding space travel, or developing next-generation chemical reactors—the complexity of their engineering requirements increases exponentially.
Custom flanges are critical in such projects because they allow for:
Precise Alignment: Ensuring that critical components align perfectly even when working within very tight spatial constraints.
Unique Stress Management: Designing flanges that can absorb, distribute, or redirect mechanical and thermal stresses without compromising system integrity.
Optimized Flow Dynamics: Custom bore sizes and shapes can significantly reduce turbulence and energy loss in fluid transport systems.
Complex systems require equally sophisticated solutions, and custom flanges are an essential piece of the puzzle in ensuring these systems operate efficiently, safely, and reliably.
Industry-Specific Standards and Certifications
Each industry comes with its own set of standards and certifications that manufacturers must meet to ensure safety, performance, and regulatory compliance. For example:
Aerospace and Defense: Requires compliance with standards such as AS9100 and military specifications (MIL-SPEC).
Oil and Gas: Must adhere to American Petroleum Institute (API) standards and pressure equipment directives (PED).
Pharmaceutical and Food Processing: Require compliance with sanitary standards like 3-A Sanitary Standards and FDA regulations.
Custom flange solutions make it easier to meet these specific certifications because they can be designed and tested from the ground up to satisfy particular requirements. Manufacturers can select the right materials, implement proper surface finishes, and incorporate quality assurance processes that align with industry expectations.
Moreover, documentation, traceability, and material certifications are easier to control and verify when flanges are custom manufactured for a particular project, ensuring hassle-free compliance audits and inspections.
Limitations of Off-the-Shelf Components
Off-the-shelf components, while cost-effective for simple applications, have serious limitations when applied to complex or mission-critical systems:
Size and Shape Constraints: Standard flanges may not fit into custom-built systems, leading to forced design compromises.
Performance Gaps: Standard materials and designs might not meet the required operating conditions, leading to early failures.
Increased Assembly Time: Modifications to standard components to make them fit or perform adequately can lead to costly, time-consuming rework.
Compromised System Efficiency: Non-optimized connections can introduce inefficiencies in flow systems, increase vibration, or create weak points under stress.
Custom flange solutions eliminate these limitations by offering purpose-built designs that enhance, rather than hinder, system performance. They allow engineers to innovate freely, knowing that their connection components will be every bit as robust and reliable as the systems they support.
Key Industries Driving Custom Flange Development
Aerospace and Defense
The aerospace and defense sectors have long been pioneers in demanding high-performance custom components. In these industries, flanges must withstand extreme conditions:
High Altitude: Pressure differentials and extreme temperatures.
High Vibration: Components must remain secure and leak-proof under continuous vibration.
Weight Constraints: Every gram matters; lightweight yet strong materials like titanium and advanced composites are often needed.
Custom flanges in aerospace are typically produced to extremely tight tolerances and undergo rigorous non-destructive testing (NDT) to ensure flawless performance. In defense applications, flanges might also incorporate stealth technology elements, such as specialized coatings or materials that reduce radar signatures.
The need for reliability, safety, and mission success drives continuous innovation in custom flange development for these industries.
Oil, Gas, and Energy Sectors
The oil, gas, and broader energy sectors operate in some of the harshest and most unpredictable environments on the planet. Whether deep underwater, in arid deserts, or amid arctic tundra, the infrastructure in these industries must be incredibly robust. Custom flange solutions are vital to ensuring system integrity and safety in such extreme conditions.
In offshore drilling, for example, custom flanges are engineered to withstand:
Extreme Hydrostatic Pressure: Flanges must maintain a perfect seal at thousands of feet below sea level.
High Corrosion Risk: Constant exposure to saltwater demands specialized materials like duplex stainless steels, Inconel, or Hastelloy.
Complex Assembly Requirements: Equipment designs often require flanges with specific angles, bore shapes, or custom bolt patterns.
Similarly, in refinery and pipeline operations, flanges must handle high temperatures, pressure surges, chemical exposure, and long operational cycles. Standardized solutions might work for basic systems, but custom flanges are indispensable in high-stakes projects where failure is not an option.
In renewable energy—particularly in wind, geothermal, and hydrogen sectors—custom flanges are developed to meet novel engineering challenges. For example, hydrogen transport systems require specialized sealing properties and materials that prevent hydrogen embrittlement, something standard flanges simply aren't equipped to handle.
The demand for reliable, durable, and efficient connections in the energy sector is accelerating the development and deployment of custom flange solutions globally.
Pharmaceutical and Biotechnology
The pharmaceutical and biotech industries have highly specific requirements when it comes to piping and process equipment. Cleanliness, sterility, and contamination prevention are paramount, and any component—even a flange—must comply with rigorous standards such as:
3-A Sanitary Standards
FDA Regulations
cGMP (Current Good Manufacturing Practices)
Custom flanges in these sectors often feature:
Smooth, Crevice-Free Surfaces: To prevent microbial growth and facilitate easy cleaning.
Sanitary Design Elements: Such as tri-clamp fittings and orbital weld compatibility.
Special Surface Finishes: Polished to low Ra values to maintain hygienic standards.
In biotech systems, where fluids might be highly sensitive biologics or active pharmaceutical ingredients (APIs), maintaining integrity through custom-designed flanges ensures that product quality is preserved, and cross-contamination risks are minimized.
Furthermore, the rise of modular pharmaceutical production facilities has led to the need for flanges that are quick to assemble and disassemble, sterilizable in place (SIP), and compatible with clean-in-place (CIP) processes. Custom flange solutions tailored to these exacting needs make the difference between compliance and shutdown, between efficient production and costly recalls.
Advantages of Custom Flange Solutions
Enhanced Performance and Reliability
When every component is designed with the specific system in mind, performance improves dramatically. Custom flanges are engineered for the exact stress, pressure, temperature, and environmental conditions they'll face. This tailored approach leads to components that are:
Stronger: Materials and geometries are optimized for maximum durability.
Safer: Custom designs eliminate weak points and potential failure areas.
More Efficient: Optimized for flow, pressure containment, and thermal performance.
Because they are purpose-built, custom flanges reduce the chance of system failure, leaks, or inefficiencies. This reliability is crucial in industries like aerospace or nuclear power, where even a minor malfunction could lead to catastrophic outcomes.
In addition to physical reliability, custom flanges also offer predictability. Engineers know exactly how the component will perform because it’s been tested or simulated for those exact conditions. This level of certainty is hard to achieve with off-the-shelf parts that were designed for general use, not a specific mission.
Cost Efficiency Over the Project Lifecycle
While it’s true that custom components can have higher upfront costs than standard ones, they often offer significant cost savings over the entire project lifecycle. Here’s how:
Fewer Failures and Downtime: Custom flanges last longer and are less likely to fail unexpectedly.
Reduced Maintenance Costs: Better materials and fitment reduce wear and corrosion.
Faster Installation: Custom fittings reduce the need for field adjustments or system redesign.
Optimized Performance: Better efficiency in fluid or gas transport leads to energy savings.
Over time, these benefits add up. Projects with custom flange solutions tend to experience smoother commissioning, lower operational costs, and fewer emergency shutdowns. In many cases, the ROI on custom flange investment becomes evident within months of deployment.
Moreover, many custom flange suppliers offer lifecycle support, including replacement parts, re-certification services, and ongoing consultation. This long-term partnership model provides ongoing value far beyond the initial purchase.
Integration with Advanced Technologies
As the industrial landscape becomes more digitized and automated, flanges are no longer just passive connection points. In some systems, they serve as integrated nodes for monitoring, control, or diagnostics. Custom flange solutions are increasingly being designed with advanced features such as:
Sensor Integration: Embedding pressure, temperature, or flow sensors directly into flange assemblies.
Smart Coatings: Coatings that change color or properties when exposed to certain conditions (e.g., corrosion indicators).
Electromagnetic Compatibility: Flanges designed to protect sensitive instrumentation from electromagnetic interference.
In fields like smart manufacturing, Industry 4.0, and the Industrial Internet of Things (IIoT), these enhancements are not optional—they’re expected. Custom flanges help bridge the gap between mechanical components and digital infrastructure, enabling smarter, more responsive systems.
These intelligent flange designs are being adopted across high-tech industries, from semiconductor manufacturing to nuclear energy, and represent a bold step into the future of industrial engineering.
Materials and Technologies Used in Custom Flange Manufacturing
Specialty Metals and Alloys
The choice of materials is central to the success of a custom flange solution. Standard carbon steel may suffice for general applications, but specialized industries require more advanced materials to cope with extreme conditions.
Some commonly used materials include:
Duplex and Super Duplex Stainless Steels: Excellent strength and corrosion resistance.
Titanium Alloys: Lightweight, extremely corrosion-resistant, especially in marine and chemical applications.
Nickel Alloys (Inconel, Monel, Hastelloy): Superior performance at high temperatures and in highly corrosive environments.
Aluminum Alloys: Ideal for aerospace and lightweight automotive applications.
Tantalum and Zirconium: Used in highly corrosive chemical processes.
These materials are selected not only for their physical properties but also for their weldability, machinability, and availability. In some cases, multi-material flanges are also produced, with dissimilar materials joined together through advanced metallurgical processes to optimize performance.
Advanced Manufacturing Techniques
Producing custom flanges requires more than traditional machining or forging—it demands precision, flexibility, and innovation. Modern manufacturers utilize a variety of advanced manufacturing techniques to create high-performance custom flange solutions:
CNC Machining: Allows for extremely accurate cutting and shaping, ideal for tight-tolerance applications and complex geometries.
Additive Manufacturing (3D Printing): Emerging as a solution for prototyping or producing low-volume, highly complex flanges. Especially useful for internal channels, lightweight structures, or custom cooling paths.
Investment Casting: Enables the creation of intricate flange shapes using high-performance alloys with smooth surface finishes and minimal material waste.
Hot Isostatic Pressing (HIP): A process that applies high pressure and temperature to metal powders, creating parts with exceptional density and mechanical properties.
Water Jet and Laser Cutting: Ideal for creating precise bolt patterns and flange outlines, especially in sheet or plate materials.
By integrating these techniques, manufacturers can offer flanges that are not only tailored to their specific use case but also optimized for performance and longevity. These processes also ensure repeatability, making them ideal for batch production in highly regulated industries.
Moreover, computer-aided design (CAD) and finite element analysis (FEA) software are used throughout the development process to simulate stress loads, thermal expansion, and other performance metrics—ensuring that the final flange performs as intended, under the most rigorous conditions.
Surface Treatments and Coatings for Durability
Custom flanges often operate in highly aggressive environments, which makes surface treatment a critical step in the manufacturing process. The right coating or surface modification can significantly enhance a flange’s lifespan, performance, and resistance to environmental challenges.
Here are some commonly used treatments:
Passivation: Used primarily on stainless steel, it removes surface contaminants and enhances corrosion resistance.
Electropolishing: Provides a mirror-like finish that is ideal for sanitary or high-purity applications like pharmaceuticals and food processing.
Powder Coating: Offers a durable, decorative finish with excellent resistance to chipping, scratching, and fading.
PTFE (Teflon) Coating: Highly resistant to chemicals, moisture, and temperature extremes, ideal for chemical processing industries.
Zinc Plating and Galvanizing: Commonly used for carbon steel flanges to prevent rust in atmospheric conditions.
Thermal Spray Coating: Applies layers of protective materials such as ceramics or metals to withstand abrasion and corrosion in high-temperature environments.
These coatings are not just protective—they can also enhance the functionality of the flange. For example, a conductive coating can help with electromagnetic shielding in sensitive electronics, while a non-stick surface may improve cleanability in food-grade applications.
By carefully selecting the appropriate treatment, custom flange manufacturers ensure the components can operate for years without degradation, even in the toughest service conditions.
Conclusion
The rise of custom flange solutions reflects a broader trend in engineering toward precision, adaptability, and innovation. As industries continue to evolve and expand into more extreme and demanding environments, the limitations of standard components become increasingly clear. Custom flanges address these limitations head-on, offering a tailored approach that improves performance, ensures safety, and reduces long-term costs.
From aerospace to pharmaceuticals, oil and gas to biotechnology, the demand for custom flange designs is being driven by complex requirements and high-performance standards. These flanges are not only stronger and more reliable but also smarter—designed to integrate with digital systems, withstand environmental pressures, and deliver unmatched durability.
As technology continues to progress, the collaboration between design engineers, material scientists, and flange manufacturers will play a pivotal role in shaping the next generation of infrastructure, transportation, and manufacturing. In this era of customization and specialization, custom flanges aren’t just a niche solution—they’re a necessity.
5 Unique FAQs
Q1: What makes a flange “custom” instead of standard?A1: A flange is considered custom when it’s manufactured to unique specifications that differ from industry-standard dimensions, materials, or designs. This includes custom sizes, bolt patterns, materials, or performance characteristics.
Q2: Are custom flanges more expensive than standard ones?A2: While the initial cost of custom flanges may be higher, they often lead to savings over time due to reduced failures, lower maintenance, and better system efficiency.
Q3: How long does it take to manufacture a custom flange?A3: Lead times can vary depending on complexity and materials but typically range from 2 to 8 weeks. Some advanced shops offer rapid prototyping or expedited delivery for urgent needs.
Q4: Can custom flanges be certified to industry standards?A4: Yes, custom flanges can be designed and tested to meet or exceed specific industry certifications, including ASME, API, ISO, and FDA standards, depending on the application.
Q5: Which industries benefit most from custom flange solutions?A5: Key industries include aerospace, oil and gas, defense, pharmaceutical, biotech, food processing, chemical manufacturing, and energy—especially in applications requiring extreme performance or regulatory compliance.
Commentaires