Not All Threaded Connectors Are Equal: A Manufacturer’s Guide to Industry Grades
- huasenmetalcast
- May 16
- 15 min read
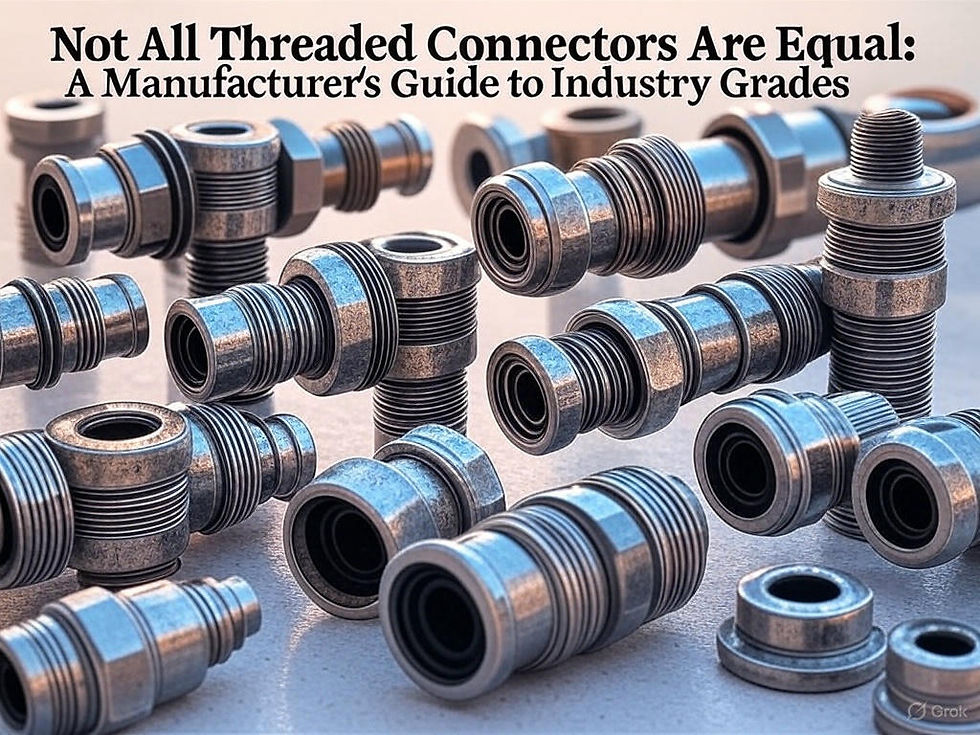
Introduction to Threaded Connectors
Understanding the Purpose of Threaded Connectors
Threaded connectors are the unsung heroes of industrial and mechanical engineering. Whether in aircraft, automotive engines, pipelines, or household plumbing, they serve a simple yet crucial purpose—creating secure, reliable, and often pressure-tight joints between components. Their design may seem basic at a glance—spiraled ridges (threads) that mesh together—but the role they play in system integrity is monumental.
From withstanding thousands of pounds of hydraulic pressure to holding parts together in jet engines, threaded connectors come in a variety of types and grades, each engineered for specific use cases. Some are designed for temporary assemblies, others for permanent fixtures; some handle high heat, others resist chemical corrosion. But the thing they all have in common is this: not all are created equal.
Choosing the right threaded connector is more than just matching thread sizes. It involves a deep understanding of industry standards, material science, engineering tolerances, and environmental factors. And that’s where grades come in. Each threaded connector has a grade—a measure of its material quality, performance characteristics, and manufacturing precision.
As a manufacturer, understanding these grades isn't just beneficial—it's essential. It’s what separates safe, reliable performance from catastrophic failure.
Why Quality and Grade Matter
So, why should manufacturers and engineers pay attention to connector grades? Because a connector’s grade is a direct reflection of its:
Mechanical strength
Corrosion resistance
Thread precision
Temperature and pressure tolerance
Durability over time
Low-grade connectors can compromise entire systems. Imagine a pressure valve on an oil rig giving out due to thread fatigue, or a misfitting connector causing fuel leaks in an aircraft. These aren’t just costly mistakes—they're potential disasters.
On the other hand, over-specifying a connector grade can be just as problematic. Using aerospace-grade titanium connectors in a standard plumbing system isn't only unnecessary—it’s a waste of budget and resources.
That’s why grade matching is so important. It ensures that connectors are:
Fit for purpose
Cost-effective
Reliable over time
In short, the right grade can mean the difference between optimized performance and total failure.
Threaded Connector Grading Explained
Overview of Thread Grades and Standards
When you hear terms like Grade 2, Grade 5, or ISO Class 10.9, you're looking at more than arbitrary labels. These are standardized grades that tell you exactly how a threaded connector will perform under stress, temperature, and corrosion conditions.
Here’s a quick breakdown of some common grading systems:
SAE Grades (U.S.): Grade 2 (low strength), Grade 5 (medium strength), Grade 8 (high strength)
ISO Metric Grades: 8.8, 10.9, and 12.9 – with 12.9 being among the strongest
ASTM Specifications: Often used in construction and structural applications
ASME/ANSI Standards: Used widely in machinery, these often specify tolerance and fit classes
Each grade typically defines tensile strength, yield strength, elongation, and surface hardness. For instance, a Grade 8 bolt under SAE standards has a minimum tensile strength of 150,000 psi, making it suitable for high-stress environments like automotive suspension systems.
But beyond numbers, these grades serve as a universal language between engineers, procurement officers, and manufacturers. When everyone speaks the same grading standard, it reduces confusion, ensures consistency, and prevents costly mismatches.
Industry-Specific Grading Systems (SAE, ISO, ASME, etc.)
Every industry has its own go-to grading system. Aerospace prefers AS9100 and NAS standards. Automotive relies heavily on SAE J429. Construction uses ASTM A307 for structural bolts. Knowing which system applies to your application is just as important as the grade itself.
Here’s how they typically stack up:
SAE J429: Used for automotive fasteners; covers Grades 2, 5, and 8
ISO 898: Used for metric fasteners; includes Classes 8.8, 10.9, 12.9
ASME B1.1/B1.13M: Focuses on thread fit and geometry
API and NPT Standards: Used for threaded pipe connectors in oil and gas
Quality manufacturers often cross-reference these standards in their product specs, ensuring compatibility across international systems. This is especially vital in global supply chains, where a connector manufactured in Germany might be installed on equipment assembled in Texas.
Materials and Their Impact on Grades
Common Materials Used in Manufacturing Threaded Connectors
The material of a threaded connector is as critical as its grade. It dictates not only the strength and durability but also how the connector responds to environmental factors like moisture, temperature extremes, and chemical exposure. Manufacturers typically choose materials based on the application environment and required mechanical properties.
Here are some of the most commonly used materials in threaded connectors:
Carbon Steel: Strong and cost-effective, ideal for general-purpose applications. Often used in Grade 2, 5, and 8 bolts.
Stainless Steel: Excellent corrosion resistance. Grades like 304 and 316 are popular in marine, food processing, and medical industries.
Alloy Steel: Enhanced strength and toughness. Common in high-grade applications such as aerospace and automotive.
Brass: Good corrosion resistance and electrical conductivity. Used in plumbing and electronics.
Titanium: Ultra-light, corrosion-resistant, and incredibly strong. Used in aerospace and medical implants.
Aluminum: Lightweight and corrosion-resistant, though not as strong as steel. Preferred in low-stress applications where weight savings are crucial.
Each of these materials affects the grade and performance capabilities of the connector. For instance, a stainless-steel connector may have great corrosion resistance but might not meet the same tensile strength requirements as a high-carbon alloy steel counterpart.
Material Strength vs. Corrosion Resistance
When evaluating connector grades, it’s essential to balance two competing factors: material strength and corrosion resistance.
High-strength materials like Grade 8 carbon steel or Class 12.9 alloy steel offer superior load-bearing capacity but may rust if not properly treated.
Corrosion-resistant materials like stainless steel or brass may lack the tensile strength of hardened steels but will last longer in harsh environments.
This is why many manufacturers apply coatings and platings (e.g., zinc, phosphate, Teflon) to steel connectors—so they get the best of both worlds: strength and protection.
Choosing the wrong balance can result in either premature corrosion (leading to system failure) or structural weaknesses (leading to breakage). For example, installing low-grade galvanized bolts in a high-vibration automotive suspension system could lead to dangerous failures.
Top manufacturers test for both strength and corrosion resistance to ensure each connector meets not just theoretical specs—but real-world demands.
Grade Classifications Across Industries
Aerospace Connector Grades
In aerospace, failure is not an option. Threaded connectors here are subjected to some of the harshest environments imaginable—extreme vibration, wide temperature variations, and life-or-death pressure tolerances.
Common grade requirements:
NAS and AN Specifications: Precision fasteners often conform to National Aerospace Standards (NAS) and Army-Navy (AN) standards.
Material Usage: Predominantly titanium, Inconel, and aerospace-grade stainless steel.
Thread Classes: Usually tight class fits like 3A/3B for vibration resistance.
Manufacturers must adhere to AS9100 certification and use traceable materials with documented quality control processes. Any deviation can result in grounded flights, failed audits, and, in worst cases, catastrophic system failures.
Automotive Connector Grades
The automotive industry uses a variety of threaded connectors, from lightweight body fasteners to high-stress engine and suspension bolts. Grades are usually determined by strength requirements and exposure to environmental elements.
SAE J429 Grades 2, 5, and 8: Most common in the U.S.
ISO 8.8, 10.9, 12.9: More common in international production vehicles.
Surface Treatments: Zinc plating, phosphate coatings, or chromates to prevent rust.
Automakers rely on well-established suppliers who test for fatigue strength, shear resistance, and vibration durability. A single recall due to connector failure can cost millions and damage brand trust permanently.
Oil & Gas Industry Standards
In oil rigs, refineries, and pipelines, connectors face intense pressure, corrosive fluids, and rough handling. Grades here must account for both mechanical endurance and chemical resistance.
API Standards: API 5CT and 6A are often referenced.
NACE MR0175/ISO 15156 Compliance: Required for sour gas environments.
Material Choice: Stainless steel, duplex alloys, and Inconel.
Threaded connectors here must survive under deep-sea pressure or desert heat, often for years without replacement. Failure isn’t just expensive—it can be ecologically disastrous.
Medical and Electronic Industry Standards
In these fields, precision and cleanliness trump brute strength. Threaded connectors are often miniature, lightweight, and exposed to sterilization or electromagnetic interference.
Material: 316L stainless steel, titanium, or biocompatible polymers.
Certifications: FDA, ISO 13485, and RoHS compliance.
Performance Metrics: Cleanability, repeatability, low magnetic interference.
Even a tiny misalignment or grade misclassification can affect patient safety or lead to equipment failure in high-stakes environments.
Differences in Performance and Tolerance
Thread Pitch, Fit, and Tolerances
One of the least appreciated—but most critical—aspects of threaded connectors is the thread design itself. The grade doesn’t just determine the material—it also dictates how precisely the threads are cut.
Here’s what defines thread performance:
Thread Pitch: The distance between threads. Fine threads (UNF) hold better in vibration-prone environments, while coarse threads (UNC) are more tolerant of wear and corrosion.
Class of Fit: For example, 2A/2B fits are looser and easier to assemble, while 3A/3B fits offer more precision but require exacting tolerances.
Tolerances: Defines allowable deviations in thread profile, major diameter, and pitch diameter.
Low-grade connectors often have inconsistent thread cuts, leading to binding, stripping, or vibration loosening. High-grade ones are cut within microns of spec, ensuring tight, consistent engagement every time.
This is why certified inspection tools like thread plug gauges and optical comparators are used by quality manufacturers to validate each batch before shipping.
Load Ratings and Pressure Handling
Another direct result of connector grading is how much load or pressure the part can safely handle. The higher the grade, the higher the tensile and yield strength.
Let’s compare two common U.S. grades:
Grade 2 Bolt: 74,000 psi tensile strength; used in light-duty applications.
Grade 8 Bolt: 150,000 psi tensile strength; ideal for heavy-duty systems.
Using a lower grade in a high-stress application can lead to stretching, thread deformation, or even complete failure under load.
That’s why manufacturers rigorously test connectors under simulated conditions—including:
Axial tension tests
Shear load tests
Fatigue cycling
The goal is to ensure that each connector grade performs exactly as expected, no matter how demanding the application.
The Role of Heat Treatment and Surface Finishing
How Heat Treatment Enhances Connector Grades
Heat treatment is a crucial step in the manufacturing of high-grade threaded connectors. It’s not just about making the metal hard—it’s about tailoring its properties to withstand specific conditions such as stress, load, and fatigue.
Here’s how it works:
Hardening: The material is heated to a high temperature and then rapidly cooled. This increases tensile and yield strength, crucial for high-load applications.
Tempering: After hardening, the material is reheated to a lower temperature to reduce brittleness and improve ductility.
Annealing: Used to soften metals, relieve internal stresses, and improve machinability.
Each heat treatment process directly impacts the grade of the connector. For example, a Grade 8 connector (SAE) has undergone more intense heat treatment than a Grade 5, resulting in nearly double the strength.
Quality manufacturers tightly control these processes. They use precisely calibrated furnaces, monitor temperature profiles in real time, and often run post-treatment inspections like microhardness testing to verify consistency.
Without proper heat treatment, even the best materials can fail under stress. That’s why this process is non-negotiable for premium-grade connectors.
Surface Finishes That Improve Longevity
After heat treatment comes the finishing process, which serves two major purposes: corrosion resistance and wear protection.
Here are the most common surface treatments:
Zinc Plating: Provides basic corrosion resistance and a clean finish.
Phosphate Coating: Improves lubricity and resistance to galling.
Black Oxide: Enhances appearance and offers mild corrosion resistance.
Teflon or PTFE Coatings: Offers chemical resistance and reduces friction.
Passivation (for stainless steel): Removes surface contaminants to prevent rust.
The type of finish often correlates with the connector’s intended environment. For example, connectors used in marine applications may have multi-layer coatings with top-tier corrosion ratings.
A quality manufacturer will always specify the finish type, thickness, and purpose in the product documentation. This attention to detail is part of what separates high-grade products from cheap, unreliable ones.
Thread Classes and Fits
Unified National Thread Standards (UNC, UNF)
In the U.S., threaded connectors follow Unified Thread Standards, which include two primary thread types:
UNC (Unified National Coarse): Coarse threads are more resistant to stripping and easier to assemble, ideal for softer materials and dirty or corrosive environments.
UNF (Unified National Fine): Fine threads provide better tensile strength and are more resistant to vibration loosening, used in automotive, aerospace, and precision equipment.
Each thread also falls into a class of fit, typically:
1A/1B: Loose fit
2A/2B: Standard fit for most industrial applications
3A/3B: Precision fit, tighter tolerances
Thread class directly affects the performance and alignment of a connector. Lower-grade parts may only loosely adhere to 2A/2B standards, while high-grade connectors are often machined and verified for exact 3A/3B precision.
This precision becomes especially important in dynamic applications like aircraft or engines where vibration can work loose a poorly fitted connector.
Metric Thread Standards and Fits
Internationally, connectors often follow ISO Metric Thread Standards, which categorize threads based on diameter and pitch in millimeters (e.g., M10 × 1.5). These threads also have class fits similar to UNC/UNF:
6g/6H: Standard tolerance for external/internal threads.
5g6g/4h: Tighter tolerance for precision fits.
Just like with Unified threads, the fit impacts how well the connector withstands stress, vibration, and wear. ISO threads are commonly found in European-manufactured products, medical devices, and precision engineering applications.
A quality manufacturer producing metric connectors must comply with ISO 965 and ISO 261 standards, and often runs automated inspection processes to verify pitch diameter and thread profile accuracy.
Misconceptions About Connector Grades
Higher Grade ≠ Always Better
It’s a common assumption that a higher-grade connector is always the better choice. But that’s not always true. Grade must be matched to the application—not just selected based on strength alone.
Why? Because:
Higher-grade materials may be more brittle under impact loads.
Over-specifying can lead to unnecessary cost and supply chain delays.
High-strength connectors may require special installation tools or torque settings.
For instance, a 12.9 ISO bolt in a soft aluminum housing could damage the threads due to the hardness mismatch. Or using Grade 8 bolts in low-stress environments may simply waste money with no performance benefit.
Smart manufacturers and engineers focus on fit-for-purpose design—choosing the right grade, not the highest grade.
Overengineering and Its Pitfalls
Overengineering happens when manufacturers select ultra-high-grade connectors without truly understanding the requirements. While this may seem like a safe bet, it introduces real-world problems:
Increased cost with no added value
Compatibility issues with mating parts
Reduced availability, leading to delays
Increased weight, especially in aerospace or mobile systems
More is not always better. Engineering should aim for precision, not excess. That’s why quality manufacturers work closely with clients to right-size their connector specifications, ensuring reliability, performance, and cost-efficiency all align.
Importance of Grade Verification
Reading Product Certifications
One of the most overlooked—but essential—steps in selecting high-quality threaded connectors is grade verification through product certifications. It's not enough to take a manufacturer’s word for it—proof must be embedded in the documentation.
Key elements of a proper product certification include:
Grade designation: SAE, ISO, or equivalent standard clearly mentioned.
Material composition: Breakdown of the metal alloy used.
Heat treatment process: Description of how strength and hardness were achieved.
Dimensional tolerances: Thread pitch, diameter, and fit classes.
Test results: Tensile, yield strength, and fatigue test documentation.
Top-tier manufacturers offer Material Test Reports (MTRs) or Certificates of Conformance (CoC) with every shipment. These aren’t optional documents—they’re your guarantee of grade accuracy.
Without these records, there's no way to confirm whether a bolt labeled "Grade 8" actually meets the required performance benchmarks. And in industries where safety, durability, and compliance matter, guessing is simply not an option.
How to Verify Manufacturer Claims
Verifying a manufacturer's grade claims involves more than just reading a datasheet. Here’s a process savvy buyers follow:
Request Sample Parts: Ask for samples with documentation to inspect physical and thread characteristics.
Ask for Third-Party Certifications: Ensure components meet ISO, SAE, or API standards and are validated by external auditors.
Conduct Independent Lab Testing: For mission-critical applications, run your own metallurgical or mechanical tests.
Review QA Procedures: Understand how the manufacturer inspects and grades their connectors internally.
Check Traceability: Good suppliers will be able to tell you exactly where the raw material came from, and every process it went through.
If a manufacturer hesitates or avoids transparency, that’s your cue to walk away.
Case Studies: Choosing the Right Grade for the Job
Industrial Application: Structural vs. Fluid System Connectors
Let’s look at two scenarios. In a structural steel framework, engineers used Grade 5 bolts because of their reliable strength-to-cost ratio. However, when the structure expanded to support fluid systems under pressure, those same bolts began to fail.
The issue? The Grade 5 connectors didn’t have the seal integrity or corrosion resistance needed for fluid systems.
They switched to stainless steel ISO 8.8 connectors with better sealing properties and enhanced surface finishing. Problem solved.
This case highlights a crucial lesson: application dictates grade. Structural and fluid systems have entirely different demands—and using one connector type for both is a recipe for failure.
Precision Application: Lab and Medical Equipment
In a clean lab environment, a firm developing diagnostic machines originally spec’d out standard metric bolts. But these fasteners showed micro-corrosion after repeated sterilization, leading to breakdowns in sensitive equipment.
They then shifted to 316L stainless steel, ISO 10.9 grade connectors—designed for corrosion resistance and precision fit. The result? Increased uptime, cleaner assembly lines, and a 25% boost in device longevity.
This case proves that in sensitive environments, choosing the right grade ensures both performance and reliability, without compromise.
Manufacturer Best Practices
Internal Grade Verification Processes
Quality manufacturers don’t guess—they verify. Their production lines are built around grade integrity. Here’s what that process usually involves:
Batch testing of raw materials using spectrometers and hardness testers
On-site inspection of thread geometries and fits
Stress testing of sample parts from every production lot
Documentation logs that trace back to every material source and machine run
This isn’t just good practice—it’s standard operating procedure for manufacturers who want to deliver on spec, every time.
Training Staff on Grade Differentiation
Even the best manufacturing systems need knowledgeable people to run them. That’s why high-end suppliers invest in regular training programs that teach their workforce:
How to read thread and material grades
How to inspect threads under magnification
How to detect plating or material defects
When to escalate for rework or rejection
A trained eye can catch what machines miss. And in industries where every detail matters, human oversight is still irreplaceable.
Working with Certified Suppliers
Benefits of Choosing Grade-Certified Vendors
Certified suppliers offer more than paperwork—they offer peace of mind. When a vendor is ISO, AS9100, or API Q1 certified, it means they’ve passed audits that verify their commitment to quality.
Working with certified manufacturers also gives you:
Faster quality approvals
Fewer field failures
Easier traceability
Better documentation for regulatory compliance
It simplifies life for engineers, project managers, and procurement teams alike.
Auditing Suppliers for Compliance
Choosing a supplier is one thing—maintaining trust is another. Smart companies periodically audit their vendors for continued compliance.
Here’s what to look for:
Are quality control procedures being followed?
Are all inspection tools calibrated and used correctly?
Are product certificates current and accurate?
Is staff adequately trained on standards and tolerances?
Annual or biannual audits help ensure your supplier doesn’t get complacent. It keeps the bar high and the risks low.
Cost vs. Quality Trade-Offs
Long-Term Costs of Using Low-Grade Connectors
Low-grade threaded connectors might save a few dollars upfront—but they cost more in the long run. How?
Increased downtime from failures
Higher replacement frequency
Compounded labor costs
Potential legal or safety liabilities
A $1 bolt might end up costing $10,000 in damage if it fails in a critical system. That’s the true cost of cutting corners on grade.
Balancing Budget and Performance Needs
That said, you don’t always need the highest-grade connector available. The goal is to match your needs to the appropriate grade:
Use Grade 2 or 5 for low-stress, dry environments.
Use Grade 8 or ISO 10.9/12.9 for high-stress or high-precision systems.
Use 316 stainless or titanium where corrosion or biocompatibility is critical.
Work with your engineering team or trusted manufacturer to right-size your specs. That way, you’re not overpaying—but you’re not compromising either.
Innovations in Connector Grades
Hybrid Material Grades
Innovation in materials is pushing connector grades to new heights. Hybrid materials—combinations of metals and coatings—are allowing manufacturers to tailor connectors for multi-purpose use cases.
Examples include:
Steel core with Teflon coating for chemical resistance and high strength.
Titanium with carbon fiber casing for lightweight, corrosion-proof applications.
These hybrid grades are redefining performance metrics, offering engineers new levels of flexibility in design.
Smart Grading with Embedded Quality Tags
Welcome to the future: smart connectors. Some high-tech manufacturers are embedding QR codes or RFID tags into connectors. These contain:
Manufacturing history
Test results
Grade info
Traceability data
With a quick scan, field technicians can verify a part's integrity instantly. This eliminates uncertainty and improves accountability, especially in regulated industries.
As this technology spreads, expect to see more “self-identifying” connectors entering the mainstream.
Conclusion
Threaded connectors are everywhere, but not all are created equal. Grade isn’t just a number—it’s a story of material science, engineering precision, and manufacturing discipline. The right grade ensures safety, performance, and longevity. The wrong one invites risk, failure, and costly rework.
Manufacturers who understand grade systems, material behavior, and industry standards can offer better solutions, avoid failures, and build trust with their customers. Whether you’re sourcing for aerospace, automotive, medical, or industrial applications, matching the right connector grade to the job is critical.
So, next time you spec a connector—don’t just ask about thread size. Ask about grade. Because when it comes to quality, details make all the difference.
FAQs
What is the difference between SAE and ISO connector grades?
SAE uses numerical grades (e.g., Grade 2, 5, 8) commonly in the U.S., while ISO uses classes like 8.8, 10.9, and 12.9 internationally. Both refer to strength and performance but follow different testing standards.
Can I use a higher-grade connector in place of a lower one?
Technically yes, but it’s not always wise. Over-specifying may cause fitment or compatibility issues, especially with softer materials or less precise threads.
What is the most corrosion-resistant grade of threaded connector?
316L stainless steel and titanium are among the most corrosion-resistant. For extreme environments, consider duplex stainless or Inconel alloys.
Are all stainless-steel connectors considered high-grade?
Not necessarily. Stainless steel offers corrosion resistance but comes in various grades. Only specific types like 304, 316, or hardened versions offer high strength and grade certifications.
How do I know what grade connector my project needs?
Consult with a certified manufacturer or engineer. They’ll consider your application’s load, temperature, corrosion exposure, and lifespan requirements to recommend the right grade.
Comments